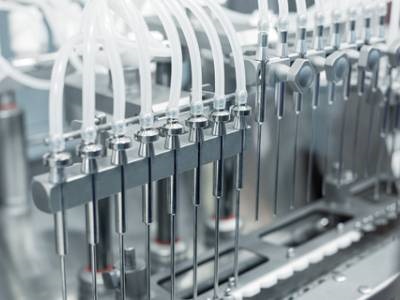
by Mihir Kumar Patel, Application Specialist, Single Use Technologies, Pall Life Sciences
Single-use filling needles manufactured from either polyether ether ketone (PEEK) or stainless steel have kept pace with advances in manufacturing, and proven themselves across a broad range of filling applications from liquid injectable pharmaceuticals to biologics and vaccines. This versatility is not their only advantage. As part of an autoclavable or gamma irradiated single-use fluid path, sterilization of single-use needles is simple. A completely disposable polymeric solution, however, removes the obvious cost and time associated with cleaning validation and as such is an attractive alternative to stainless steel. The potential for vial damage due to needle strikes is also significantly reduced thanks to the inherent flexibility of polymeric materials. However, the challenge, as with any needle within a biopharmaceutical filling process, is in reducing the potential for a needle to clog or drip and cause costly interruptions that can so easily derail the most well controlled of filling processes.
So, why do filling needles clog or drip and how can we effectively reduce these effects? These questions can be answered when we take a closer look at needle design, needle size and the physical attributes of a final formulation.
Read more on Labcompare.