Quality control managers are under constant pressure to conduct analyses as efficiently and cost-effectively as possible. In certain industries, such as paints and coatings and food, rheological testing in oscillation mode is critical, yet it can be a particularly costly part of the quality control process.
Oscillatory tests can determine the viscous and elastic properties of a material and are considered the ideal method with which to examine storage behavior and shelf-life, primarily because they are deemed to be nondestructive to complex materials—during an experiment, the microstructure of a sample is not disturbed by the forces applied. Rheological testing in oscillation mode can also be used to investigate phase transitions and crystallization and curing processes.
Effective oscillatory testing, however, requires a rheometer with a low-friction bearing system, minimal instrument inertia and a highly dynamic motor. Using a robust rotational rheometer with a mechanical-bearing—rather than an air-bearing rheometer, which is standard for oscillatory testing—quality control personnel can improve efficiency while achieving optimal results.
Stress mode versus deformation mode
When performing a rheological test in oscillation, a sample can be approached in either controlled-stress (CS) or controlled deformation (CD) mode. Depending on the type of excitation, the sample responds with a deformation (in CS mode) or a stress (in CD mode). A sine curve appears when the amplitude values of the applied deformation or stress signal are low. Tests that are performed in this way, i.e., in the linear–viscoelastic range, are considered nondestructive, with the applied forces being too low to alter a sample’s microstructure.
The applied sinusoidal and response signals show a phase shift between 0° and 90°, depending on the type of sample. A phase shift of 90°, which is exhibited in samples such as water or mineral oils, indicates that a sample is purely viscous, with no elastic response. Alternatively, a phase shift of 0° signifies that a sample is purely elastic, with no viscous response; this is the case with steel or thermoset polymer materials, for example. Most complex materials, however, exhibit both viscous and elastic behavior—known as viscoelastic behavior.
Figure 1 – Thermo Scientific HAAKE Viscotester iQ rheometer.Oscillatory measurement techniques are ideal for studying a material’s viscosity and elasticity. The shelf-life of a material can be examined using oscillatory testing, as can various phase transitions such as melting, curing and crystallization that take place under different conditions. Measurements like amplitude sweep, frequency sweep and time sweep can be made when an oscillatory excitation force is applied to a sample using a Thermo Scientific HAAKE Viscotester iQ mechanical-bearing rotational rheometer (Thermo Fisher Scientific, Karlsruhe, Germany) (Figure 1).
An oscillatory amplitude sweep is used to determine the linear–viscoelastic range of a material and to derive a yield stress. To do so, the frequency of the exciting sinusoidal signal is kept constant while the amplitude is increased gradually. The increase continues until the microstructure breaks down and the rheological material functions are no longer independent of the set parameter.
Conversely, with an oscillatory frequency sweep, the amplitude of the exciting sinusoidal signal is kept constant while the frequency is increased or decreased gradually. Frequency sweeps can ascertain whether a sample behaves like a viscous or viscoelastic fluid, gel-like paste or fully cross-linked material.
Finally, an oscillatory time sweep requires that the amplitude and frequency of the exciting sinusoidal signal is kept constant and that the rheological properties of the material are monitored over time. Time sweeps are used to examine structural changes that can occur during curing and gelification reactions as well as drying and relaxation processes.
Benefits of a mechanical-bearing rheometer
A compact, rotational rheometer equipped with a highly dynamic, electronically commutated motor allows for rotational rheological experiments in both CS and CR modes. While the bearing friction and total system inertia are much higher with a mechanical-bearing instrument, oscillatory tests in CS and CD modes are still possible within certain frequency, angular deflection and torque ranges.
A rheometer equipped with various measuring geometries—ranging from coaxial cylinders over vane-type rotors to parallel plates and cone/plate fixtures—has the flexibility to test a broad range of samples. Medium- to high-viscosity samples can be tested in oscillatory mode (see specifications/measuring range for oscillation tests with the HAAKE Viscotester iQ rheometer in Table 1).
Table 1 – Specifications of the HAAKE Viscotester iQ rheometer for oscillatory experiments
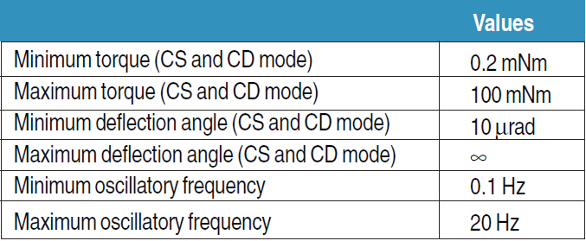
Experiments and results
Oscillary experiments were done to test the performance of the mechanical-bearing rheometer. A certified mineral oil provided by the German Calibration Service was used as a Newtonian standard fluid, and a polyisobutylene dissolved in 2,6,10,14-tetramethyl-pentadecane, provided by the National Institute of Standards and Technology (NIST), was used as a non-Newtonian reference material.
One test showed the frequency sweeps performed with the Newtonian standard fluid at varying temperatures (see results in Figure 2). The tests were done using a 35-mm parallel plate geometry with the measuring gap set to 0.5 mm. As temperature decreased, the material became more viscous and the measuring range was extended toward lower frequencies.
Figure 2 – Loss modulus G’’ and complex viscosity Iη*I as a function of the frequency for German Calibration Service Newtonian standard fluid at three different temperatures.When the viscosity data obtained was compared with the certified values for the dynamic viscosity provided by the German Calibration Service (see Table 2), the deviation from the certified viscosity was shown to be <7% for all data measured.
Table 2 – Results of frequency sweeps with German Calibration Service Newtonian standard fluid at different temperatures
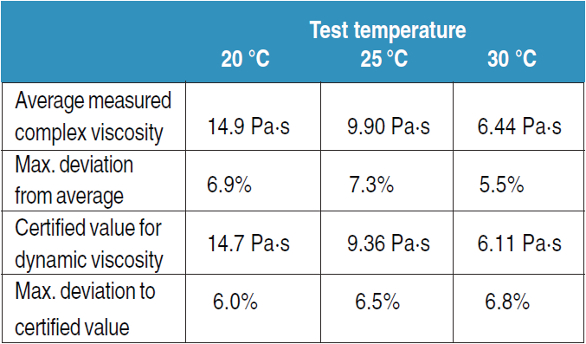
An amplitude sweep was also conducted on the non-Newtonian standard material with the mechanical-bearing rheometer and, for comparison, with an air-bearing rheometer (see Figure 3). The test on the mechanical-bearing rheometer was performed with a 60-mm parallel plate geometry with the measuring gap set to 0.5 mm, while the air-bearing rheometer test was performed with a 35-mm parallel plate geometry and the measuring gap set to 0.5 mm. The results were comparable, with the maximum difference between the two being less than 5%. The modulus data clearly allows differentiation between the linear and the nonlinear viscoelastic range of the tested standard sample.
Figure 3 – Storage modulus G’ and loss modulus G’’ as a function of the deformation γ for NIST non-Newtonian standard material at 25 °C.Frequency sweeps were performed within the linear viscoelastic range using the information obtained from the amplitude sweep. A frequency range from 0.1 to 20 Hz (the maximum for the HAAKE Viscotester iQ rheometer) was selected, with a deformation of 10%. Again, the results were comparable for the measured and certified values from the mechanical-bearing rheometer and the data provided by NIST (see results in Figure 4).
Figure 4 – Storage modulus G’, loss modulus G’’ and complex viscosity Iη*I as a function of the angular frequency for the NIST non-Newtonian standard sample at 25 °C.Results from the frequency sweep indicated <7% difference between the two calculated crossover modulus values (see Table 3).
Table 3 – Results of frequency sweeps with non-Newtonian viscosity standard at 25 °C
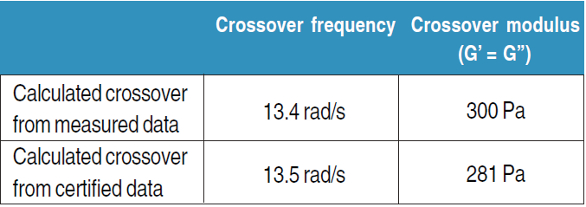
Conclusion
Oscillatory experiments on standard materials have generally been limited to high-priced rheometers with limited accessibility. The tests described in this article, conducted using the HAAKE Viscotester iQ rheometer in CD and CS modes, establish that oscillatory experiments can be done with a mechanical-bearing rotational rheometer. While there are some limitations, such as the measuring range, in comparison to a high-performance air-bearing rheometer, the mechanical-bearing rotational viscometer gives quality control personnel the ability to conduct oscillatory tests more economically without compromising the integrity of results.
Fabian Meyer is senior application specialist, Thermo Fisher Scientific, Material Characterization Products, Dieselstr. 4, 76227 Karlsruhe, Germany; e-mail: [email protected]; www.thermoscientific.com