Mercury is one of the most toxic elements in the environment. Humans are exposed to mercury through the inhalation of mercury vapor, ingestion of drinking water, and consumption of fish.1,2 A high accumulation of mercury in the body causes damage to the nervous system. In particular, the prenatal and postnatal nervous system can become compromised when a pregnant woman is exposed to a high level of mercury. Thus, analysis of mercury in the environment is critical.
One source of mercury exposure is cement, a widely used material of construction that may contain a high concentration of mercury. Slag has been investigated as an alternative to cement because it is lower in cost and contains less toxic elements. Elemental analysis in cement and slag has been tedious due to the complex matrix. Mercury analysis has not been facilitated because mercury is a toxic and volatile element. During the preparation of a sample, the concentration of mercury can be easily reduced by evaporation, and this can have a profound effect on the accurate quantitation of mercury in samples. Thus, if possible, sample preparation or manipulation should be minimized for mercury analysis.
Many investigators have reported on various techniques to analyze mercury. These include inductively coupled plasma mass spectrometry (ICP-MS),3–6 cold vapor atomic absorption spectrometry (CVAAS),7,8 flow injection-CVAAS,9 flameless atomic absorption spectrometry,10 and atomic fluorescence spectrometry.11,12
In the present work, solid samples were directly injected and heated, and then vaporized and atomized. The atomized mercury was only amalgamated with gold in the column. The amalgamated mercury was vaporized and atomized by heating after the matrix passed through the column path. Mercury absorption was then measured and its concentration accurately determined. Direct solid sampling has several advantages over solution sampling in terms of contamination risk, memory effect, and loss of analyte. When the concentration of mercury in cements and slags was compared, it was found that the concentration of mercury in cements was higher than that in slag. In addition, the concentration of Cu, As, Cd, and Pb in cements and slags was determined by inductively coupled plasma-atomic emission spectrometry (ICP-AES).
Experimental
Instrumentation
An Auto MA-2 mercury analysis system (Nippon Instruments Corp., Tokyo, Japan) was used. The sample was thermally decomposed and atomized in the heater at 850 ºC. The free mercury in the gas was collected by a gold amalgam. The amalgam was then heated to release the mercury, which was detected by atomic absorption at a wavelength of 253.7 nm. The mercury in the solid and liquid was quantitated directly without any sample dissolution or manipulation. An Arcos ICP-AES (Spectro, Essen, Germany) determined the concentration of Cu, As, Cd, and Pb in the cement and slag. Details of the instrument and operating conditions are given in Tables 1 and 2.
Table 1 - Instrument and operating conditions for Hg analyzer
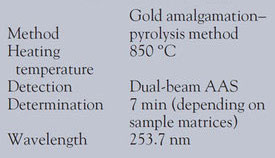
Table 2 - Instrument and operating conditions for ICP-AES
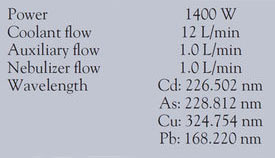
Reagents
Mercury standard solution (1000 μg/mL) (Wako, Osaka, Japan) and L-cysteine (98%) (Nacalai Tesque, Kyoto, Japan) were used. The L-cysteine was utilized as a solvent for the Hg standard solution. A 10-μg/mL Hg standard solution was first attained by diluting 1000 μg/mL Hg standard solution in 0.001% L-cysteine. Next, 0.1 μg/mL Hg standard solution was obtained from 10 μg/mL standard solution. Blank and 20, 40, and 80 μL of 0.1 μg/mL Hg standard solution were injected into the mercury analyzer for the calibration curve. To measure the concentration of mercury in the sample, each 150-mg sample was measured five times.
A standard solution of Cu, As, Cd, and Pb (1000 μg/mL) (VHG Labs, Manchester, NH) was used. Ultrapure water (18 MΩ/ cm) from a PURELAB Plus UF water purification system (ELGA, Woodbridge, IL) was used for aqua dilutions; concentrated nitric acid (Sigma-Aldrich, St. Louis, MO) was employed for sample pretreatment.
For the calibration curves, 0.1, 0.5, 1, 5, and 10 μg/mL Cu, As, Cd, and Pb standard solution were obtained from the dilution of 1000 μg/mL stock solution. For the measurement of Cu, As, Cd, and Pb, each 200-mg sample was prepared by microwave digestion and then measured three times.
Results and discussion
Table 3 - Determination of Hg by Hg analyzer
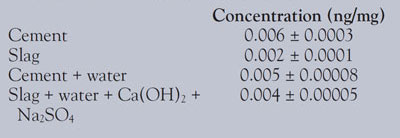
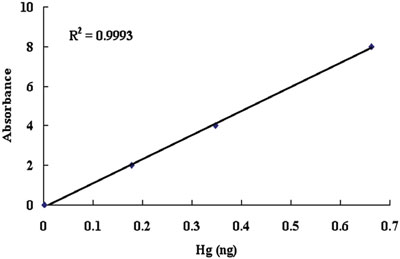
Figure 1 - Hg calibration curve.
Four samples (cement, slag, cement hardened by water, and slag hardened by calcium hydroxide and sodium sulfate) were prepared for the determination of mercury. Approximately 150 mg of powder sample was loaded into the sample container. Five replicate samples were investigated (see Table 3). The analytical calibration curve is shown in Figure 1. The concentration of mercury in slag was much lower than that in cement. It was found that slag may be a good alternative to cement because it is lower in cost and less toxic.
Table 4 - Determination of Cu, As, Cd, and Pb by ICP-AES (μg/g)
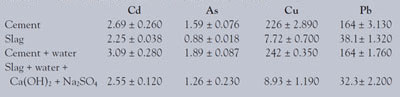
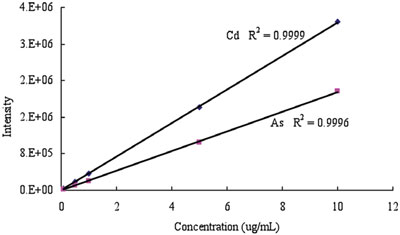
Figure 2 - Cd and As calibration curves.
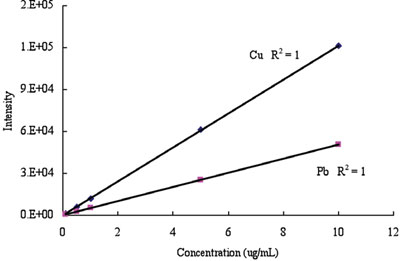
Figure 3 - Cu and Pb calibration curves.
The concentration of mercury in cement hardened by water was slightly lower than in cement due to the dilution effect. The concentration of mercury in slag hardened by calcium hydroxide and sodium sulfate was slightly higher than that in slag, but was still lower than that in cement and cement hardened by water. The increase may be due to the impurities of calcium hydroxide and sodium sulfate. At any rate, the results demonstrated that the hardened slag could be a suitable construction material.
The concentration of Cu, As, Cd, and Pb was determined by ICP-AES (see Table 4). The analytical calibration curves are shown in Figures 2 and 3. The extracted concentrations of Cu in cement and cement hardened by water were much higher than those in slag and activated slag. The concentration of As in slag was lower than that in cement, as shown in Table 4. The trace amount of As in slag hardened by calcium hydroxide and sodium sulfate may be from the impurities of calcium hydroxide and sodium sulfate. The concentration of Cd in cement was slightly higher than that in slag. The extracted concentrations of Pb in cement and cement hardened by water were also much higher than those in slag and activated slag. The results showed that slag may be a better construction material than cement due to the concentration of harmful elements.
Conclusion
The concentration of mercury in slag was significantly lower than that in cement. The concentration of mercury in slag was 0.002 ng/mg, while in cement it was 0.006 ng/mg. The concentration of mercury in cement hardened by water was slightly lower than in cement because of the dilution effect. However, the concentration of mercury in slag hardened by calcium hydroxide and sodium sulfate was somewhat higher than that in slag. The increase may be due to the impurities of calcium hydroxide and sodium sulfate.
In addition, the concentration of Cu, As, Cd, and Pb in cement and slag was determined by ICP-AES. The extracted concentrations of the four elements in cement and cement hardened by water were much higher than those in slag and activated slag.
References
- Alonso, E.V.; Cordero, M.T.; Torres, A.G.; Rudner, P.C.; Pavon, J.M. Talanta 2008, 77, 53.
- Martinis, E.M.; Berton, P.; Olsina, R.A.; Altamirano, J.C.; Wuilloud, R.G. J. Hazardous Mater. 2009, 167, 475.
- Allibone, J.; Fatemian, E.; Walker, P.J. J. Anal. At. Spectrom. 1999, 14, 235.
- Davis, W.C.; Vander Pol, S.S.; Schantz, M.M.; Long, S.E.; Day, R.D.; Christopher, S.J. J. Anal. At. Spectrom. 2004, 19, 1546.
- Legrand, M.; Lam, R.; Fontaine, M.J.; Salin, E.D.; Chan, H.M. J. Anal. At. Spectrom. 2004, 19(10), 1287.
- Sturman, B.T. J. Anal. At. Spectrom. 2000, 15, 1512.
- Hight, S.C.; Cheng, J. Food Chem. 2005, 91, 557.
- Shim, S.M.; Dorworth, L.E.; Lasrado, J.A.; Santerre, C.R. J.Food Science 2004, 69, 9.
- Murphy, J.; Jones, P.; Hill, S.J. Spectrochim. Acta Part B 1996, 51, 1867.
- Munns, R.K.; Holland, D.C. J. AOAC 1977, 60(4), 833.
- Labatzke, T.; Schlemmer, G. Anal. Bioanal Chem. 2004, 378, 1075.
- Tseng, C.M.; Hammerschmidt, C.R.; Fitzgerald, W.F. Anal. Chem. 2004, 76, 7131.
Prof. Nam is a professor, and Ms. Kim and Mr. Na are graduate students, Department of Chemistry, College of Natural Science, Mokpo National University, Muangun, Chonnam, Republic of Korea; tel.: +82 61 450 2333; fax: +82 61 450 2339; e-mail: [email protected]. Prof. Yang is a professor, Architecture Engineering Laboratory, Department of Architecture Engineering, Kyonggi University, Suwon, Kyonggi-Do, Republic of Korea. This work was supported by the Korea Science and Engineering Foundation (KOSEF) grant funded by the Korean government (MEST) (no. 20090083928).